Professional Power Tools: Selecting a Manufacturer for High-Precision Applications
- Diversitech Global
- Aug 30, 2023
- 5 min read
Updated: Feb 23, 2024
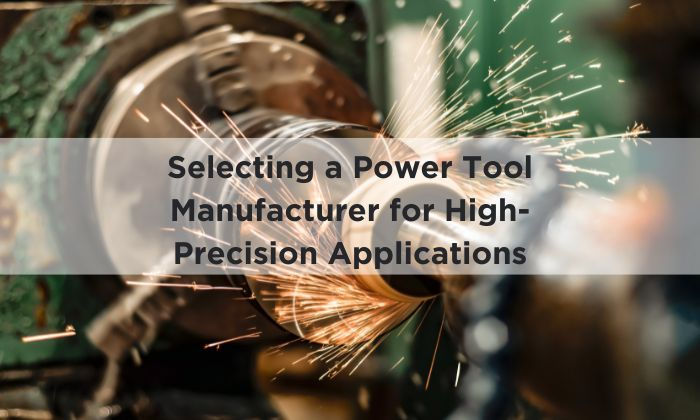
The high-stakes world of industrial applications demands tools that are not just robust and durable, but also precise and consistent. This necessitates a meticulous selection process when choosing a professional power tools manufacturer. The right manufacturer understands the intricate requirements of high-precision applications and ensures their tools deliver on these parameters. For any power tools manufacturer, understanding these high-precision requirements is pivotal as it influences every aspect of the manufacturing process, from material selection to quality control.
This comprehensive guide aims to shed light on the intricate process of manufacturing professional power tools, focusing on the importance of understanding tool requirements, selection of materials and processes, quality control measures, and insights drawn from case studies. We will also delve into the role of innovation in manufacturing, compliance standards, and the future of power tools manufacturing.
Table of Contents
Understanding Professional Power Tools Requirements
Professional power tools are designed for specific tasks and applications, each with its unique set of requirements. These requirements can be broadly categorized into functionality, durability, and user comfort. Functionality refers to the tool's ability to perform the required task efficiently and accurately. Durability involves the tool's resilience under heavy use and harsh conditions. User comfort pertains to the tool's design in terms of ergonomics and safety features.
For example, a professional-grade drill should provide precise control over drilling speed and depth, withstand repeated use without overheating or breaking down, and have ergonomic handles and safety features like an automatic cut-off switch.
Understanding these requirements helps manufacturers design and develop power tools.
that meet or exceed industry standards. It also enables them to tailor their products to the specific needs of different industries and applications.
A construction company, for instance, may require power tools that can withstand heavy-duty use and harsh outdoor conditions, while a furniture maker might prioritize precision and fine control over raw power.
Additionally, understanding power tools requirements also means considering future needs and potential technological advancements. Manufacturers must be forward-thinking, anticipating changes in industry needs and technological innovations. This proactive approach ensures their power tools remain relevant and competitive in the market.
Selecting Materials and Manufacturing Processes
The materials used in manufacturing power tools play a significant role in their performance and durability. Common materials include steel for the tool's body, carbide or diamond for cutting edges, and plastic or rubber for handles and grips. The choice of material depends on the tool's function, the conditions under which it will be used, and cost considerations.
Steel, for instance, is a durable and relatively inexpensive material that is suitable for many types of power tools. However, for cutting tools that need to maintain a sharp edge, harder materials like carbide or diamond might be more appropriate.
The manufacturing process also plays a crucial role in the tool's quality and performance. Methods such as casting, forging, and machining are commonly used in power tool manufacturing. Each method has its advantages and disadvantages, and the choice depends on factors like the tool's design, material, and production volume.
For example, casting is a cost-effective method for producing large volumes of parts but may not offer the same level of precision as machining. On the other hand, machining can produce highly accurate parts but is more time-consuming and expensive.
Moreover, advancements in manufacturing technologies are continually providing new opportunities for power tools manufacturers. Techniques like additive manufacturing (3D printing) allow for more complex designs and can reduce waste, offering potential cost savings and environmental benefits.
Related Article: American Craftsmanship: Power Tool Manufacturing
Quality Control and Precision Engineering
Quality control is a vital aspect of power tool manufacturing. It involves various tests and inspections to ensure that the tools meet the required standards of performance, durability, and safety. These can include visual inspections, dimensional checks, performance tests, and endurance tests.
For example, a dimensional check might involve measuring the size and shape of a drill bit to ensure it matches the specifications. An endurance test might involve running a power tool continuously to see how long it lasts before failure.
Precision engineering is another critical aspect of high-precision power tools. This involves designing and manufacturing tools with a high degree of accuracy, often down to fractions of a millimeter. Precision engineering requires advanced machinery and skilled operators, but the result is a tool that delivers superior performance and consistency.
For instance, a precision-engineered saw blade will cut more accurately and smoothly than a standard blade, reducing the risk of errors and rework.
Beyond these, continuous improvement is essential in quality control and precision engineering. Manufacturers should regularly review and refine their processes, striving for ever-greater efficiency and accuracy. This commitment to improvement helps maintain high standards and keeps pace with evolving industry demands and technological advancements.
Related Article: Power Tools Manufacturing: A Strategic Approach for Growth
Case Studies of High-Precision Tools Manufacturing
Case studies offer invaluable insights into the practical challenges and triumphs of manufacturing high-precision power tools. They illuminate the application of the principles discussed above, demonstrating how manufacturers surmount hurdles to produce top-notch tools.
A case study titled "Additive layered manufacturing: sectors of industrial application shown through case studies" published in the International Journal of Production Research highlights the use of additive manufacturing, also known as 3D printing, in creating high-precision models. The study mentions materials like R5 and R11, which are commonly used for high-precision models. This research demonstrates how advancements in manufacturing technologies, like additive manufacturing, allow for more complex designs and can reduce waste, offering potential cost savings and environmental benefits.
Another case study titled "Femtosecond lasers: the ultimate tool for high-precision 3D manufacturing" published in Advanced Optical Technologies presents the utilization of femtosecond lasers in various applications. One example highlighted in the research is a hole cut in a 100-μm-thick steel foil with extreme precision and minimal heat affected. This case study illustrates that innovative tools like femtosecond lasers can significantly enhance precision in tool manufacturing. Source: https://www.tandfonline.com/doi/abs/10.1080/00207540903479786
These case studies not only provide examples of successful manufacturing practices but also offer lessons that other manufacturers can learn from and apply to their operations.
Notably, case studies also serve as proof of a manufacturer's capability and credibility. By demonstrating their success in previous projects, manufacturers can build trust with potential customers and stakeholders. This can be a powerful tool in establishing and strengthening business relationships.
The Art and Science of Power Tool Manufacturing
Manufacturing professional power tools for high-precision applications is both an art and a science. It requires a deep understanding of the tool's requirements, careful selection of materials and manufacturing processes, rigorous quality control, and precision engineering. By mastering these elements, manufacturers can produce power tools that deliver exceptional performance and durability, meeting the demanding needs of professional users.
As the market for professional power tools continues to evolve, manufacturers must stay ahead of the curve by continually improving their products and processes. This involves investing in research and development, adopting advanced manufacturing technologies, and listening to feedback from users. By doing so, they can ensure their tools remain the go-to choose for professionals across various industries.
Moreover, in an increasingly digital and connected world, manufacturers must also consider the role of digital technologies and data analytics in enhancing their manufacturing processes and product offerings. Embracing digital transformation can lead to improved efficiency, quality, and innovation, ensuring they remain competitive in the industry 4.0 era.
Related Article: List of Top Power Tools Manufacturers
Comments