What Causes Manufacturing Price Fluctuations In The Hand & Power Tool Industry?
- Diversitech Global
- Mar 21
- 5 min read
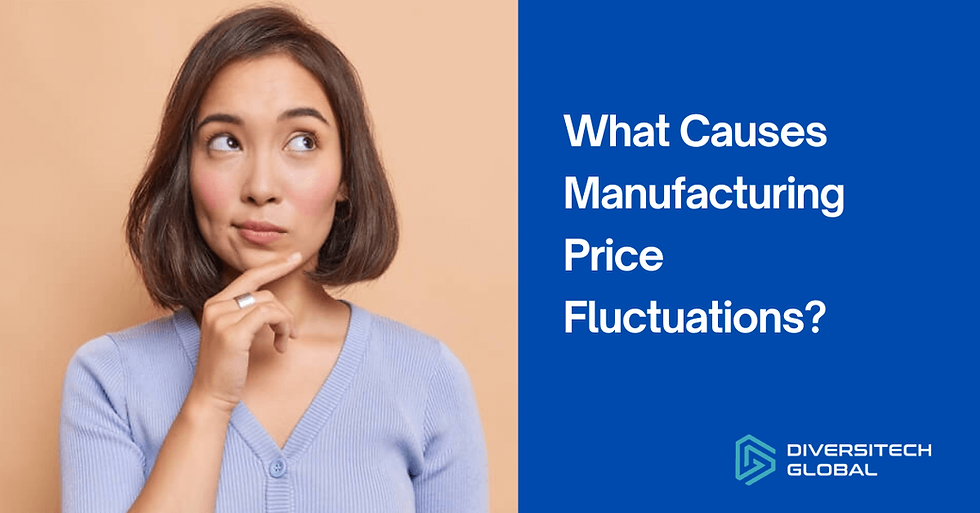
Manufacturing price fluctuations are caused by many factors. For example, it might be a good idea to produce more to increase profit margins, but if there is an oversupply, it will ultimately lead to a decrease in price.
Additionally, price fluctuations can happen for a number of reasons that have nothing to do with market forces. These include events such as pandemics, natural disasters, and political events such as war.
Table of Contents:
Basic Supply and Demand
Manufacturing prices are a reflection of demand-supply shifts from customers and clients who may change their requirements over time and purchase different products than before. A high demand for particular goods and not enough to go around leads to increased prices as manufacturers can charge according to how much their customers are willing to pay.
As of March 2025, the JPMorgan Global Manufacturing PMI, compiled by S&P Global, indicates a mixed global economic landscape. The index registered 51.5 in February 2025, reflecting a slowdown in global economic expansion, which has now reached its slowest pace in 14 months. While goods production saw its fastest growth in eight months, services activity decelerated for the second consecutive month. Cost pressures have also intensified, with input cost inflation reaching a seven-month high
US-China Trade War
The ongoing US-China trade war has significantly impacted global manufacturing costs. Tariffs imposed by the US on Chinese goods have increased expenses for manufacturers, forcing many to adjust pricing strategies, relocate supply chains, or seek cost-cutting measures to remain competitive.
To counter these rising costs, Diversitech Global, a leading hand and power tool manufacturer in China, has adopted a pricing strategy that offers products up to 30% cheaper than competitors. This approach helps offset the added costs of US tariffs, allowing businesses to maintain profitability while sourcing high-quality tools from China.
Are tariffs holding you back? Talk with us and let's strategize
The Pandemic and A Seller’s Market
Furthermore, average factory input costs increased at the third-fastest rate ever recorded during the previous ten years. This increase in pricing was primarily caused by suppliers' being able to raise prices in the face of severe shortages, which created a sellers' market for various inputs ranging from electronic components to basic raw materials utilized in products for the construction sector.
Along with the surge in demand for many products, notably in household items such as hand and power tools due to the extended lockdowns and work from home rules, the pandemic has also severely harmed production of components and logistical capacity.
Related article: Global supply chains in a post-pandemic world
Slowing Demands From Manufacturers
However, a weaker rise in new orders demand from manufacturers and a drop in consumer spending, compared to earlier in 2021, helped ease some of the strain on both supply chains and pricing.
Fewer factories were creating buffer stockpiles of inventory, which contributes in part to the decrease in demand. Producers were placing fewer orders for other inputs because they are unable to complete their production due to a shortage of crucial components.
For instance, a power tool manufacturer in China specializing in cordless drill-drivers whose supply of lithium-ion batteries is now limited will be ordering fewer switches, tool casings, steel components, and so on.
Raw Materials

Another factor that causes manufacturing price fluctuations is the shortage of materials, or commodity price changes due to market speculation. When tool manufacturers are unable to obtain enough necessary materials, they have no choice but to increase their prices to cover the production costs of more expensive sources and replacements of materials.
As our economies become more globalized and interconnected, it's becoming harder for manufacturers to find reliable sources of materials at prices that won't fluctuate.
In recent years, there has been a push towards eco-friendly manufacturing practices and protocols due to concerns about global warming and the environment.
Some companies have switched from petroleum-based plastics to bio-plastics, which use natural plant-based materials rather than fossil fuels as a base product.
Although these bio-plastics are more readily available, they can be much more expensive than traditional plastic products because of higher costs in production and quality control standards.
Suppliers in the Chain
The manufacturing industry is not just composed of companies that produce finished products; there are also many components involved in the supply chain that help build these products.
A majority of tool manufacturers rely on a small selection of suppliers for their materials or specialized parts. If a manufacturer has been using the same supplier for a long time, the supplier might pass along preferential treatment to that manufacturer.
If a supplier discontinues manufacturing niche items or services, or they close down or are bought up, manufacturers have to find an alternative source for these hard-to-find materials or essential parts, thus driving up the price of the production processes.
They might even need to pay increased prices just to continue receiving preferred service levels from existing vendors.
Underscoring the recent supply chain delays caused by the pandemic, the average suppliers' delivery times have climbed internationally at a rate unheard of in more than 25 years of survey data.
Related Article: The growth of supply chain outsourcing
Currency Exchange Rates
It should be noted that fluctuations in currency exchange rates also affect movements in materials’ prices. For example, when currency values are unstable and depreciate quickly over short periods of time, manufacturing material prices tend to rise because they’re paid in local currency while costs are incurred in foreign currency.
Fuel And Transportation
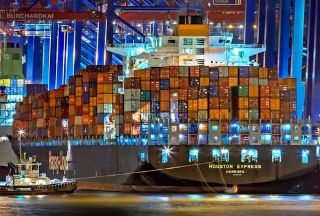
Another factor affecting material costs is the increase in fuel prices, which can translate into higher production costs because manufacturers often outsource transportation services for their goods. As recent as 2008, increased gas prices led to an average of 4 percent annual increases in shipping charges.
This doesn't include extreme conditions like strikes or natural disasters that could drive up transport costs even more quickly and severely than conventional fuel price fluctuations.
According to IHSMarkit, September 2021 saw 15 times the normal number of manufacturers, the highest proportion ever recorded, reporting higher shipping costs having contributed to higher average input prices.
Environmental Concerns
In recent years, there has been a push towards eco-friendly manufacturing practices and protocols due to concerns about global warming and the environment. Some companies have switched from petroleum-based plastics to bioplastics, which uses natural plant oils rather than fossil fuels as a base product.
Although these bioplastics are more readily available and cost effective in some cases, they can be much more expensive than traditional plastic products because of higher costs in production and quality control standards. Additionally, many customers are unwilling to pay the price for eco-friendly products and manufacturers must find a way to make up this additional cost.
Labour
Similar to supply and demand, the availability of labor will also affect the price of manufactured goods because it's a vital factor in determining selling prices.
For example, where there are lots of available workers with specific skill sets for an area or industry, businesses can offer less money for jobs as there will be plenty of applicants who are willing to work at those rates.
On the other hand, if fewer people are looking for work and the ones who are available have skills that businesses need, they will offer higher salaries in order to attract them.
Related Article: Is it really cheaper to manufacture in China?
Conclusion
A Hand and Power Tool Manufacturer must be ready for fluctuations in the market and protect themselves by hedging against these risks. Staying competitive in a global marketplace requires taking advantage of sources of expertise and guidance in chain-supply management, from product designing to final packaging and even point of sale displays.
By working directly with manufacturing strategists and chain-supply specialists with years of experience and relationships with reliable suppliers, businesses are made less vulnerable and better prepared against unpredictable events in labor or material prices which could severely affect the bottom line.
Related Article: Why China Is "The World’s Factory"
Looking to overcome the tariffs and dominate the hand & power tool market? Get started
Comments